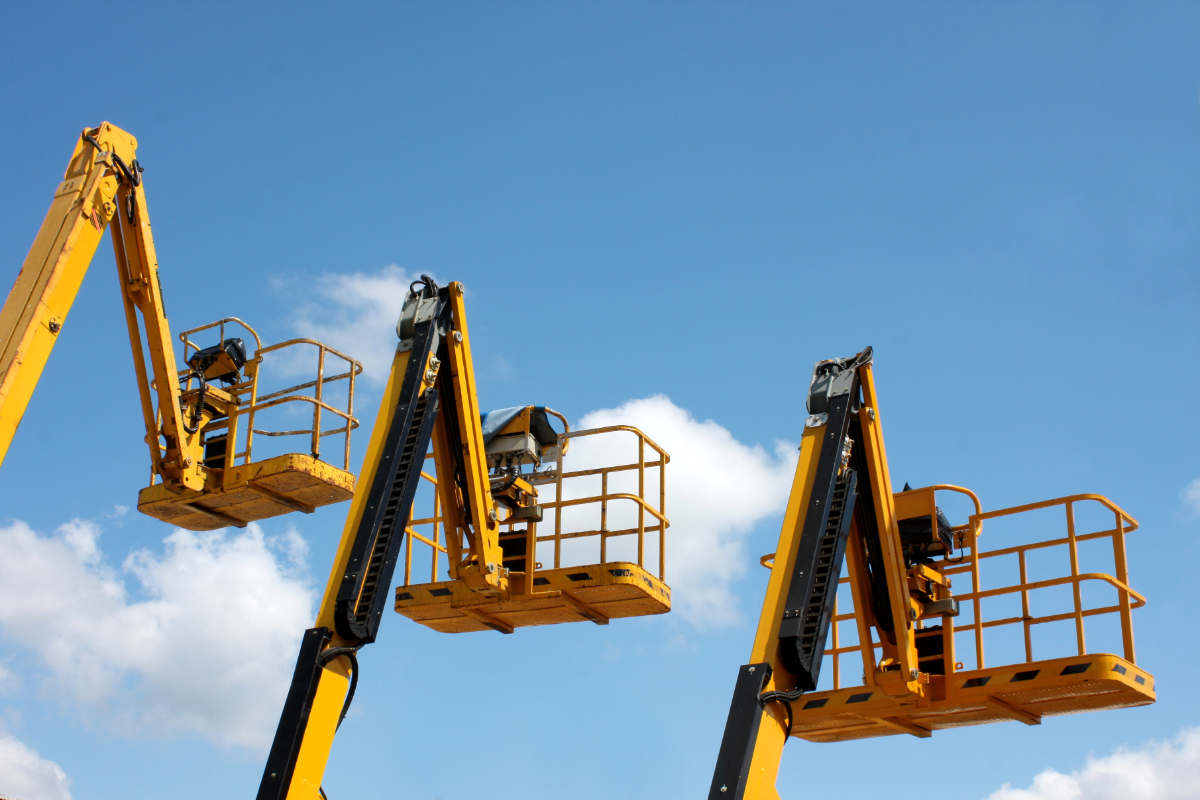
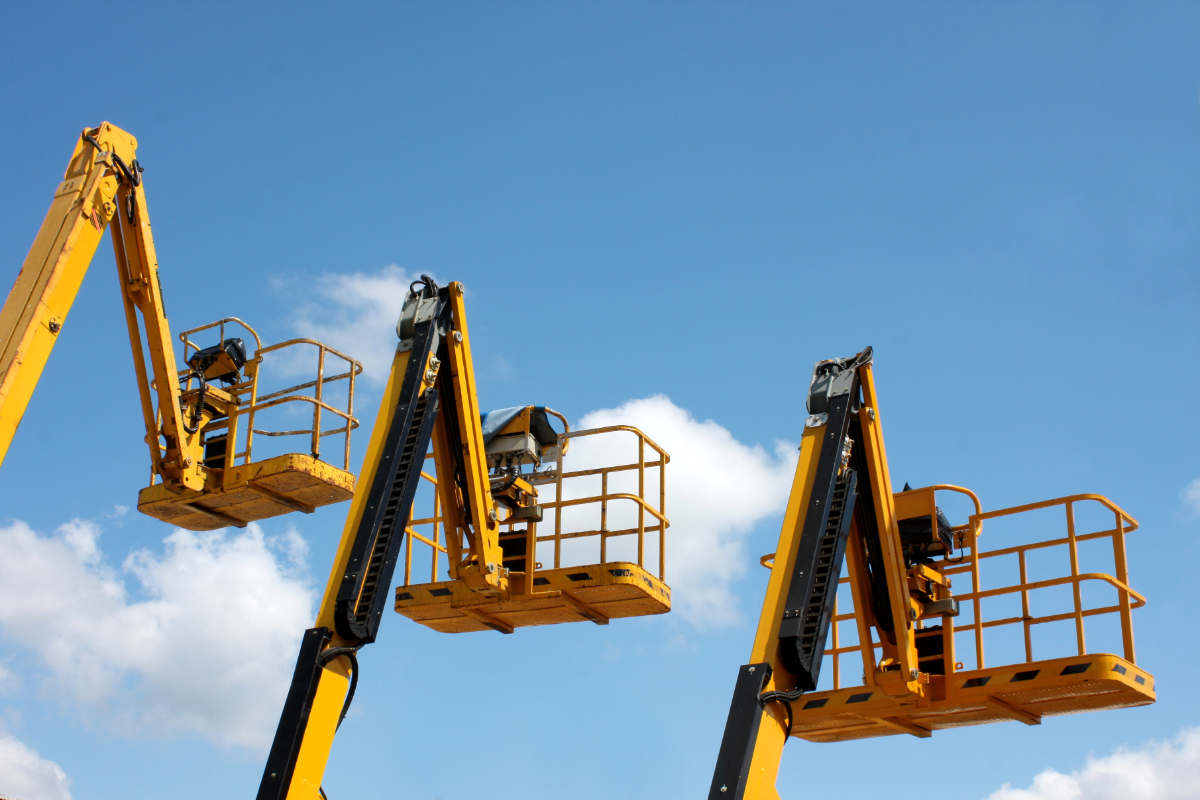
Estimated reading time: 4 minutes
Yard managers have a tough job. Keeping track of everything that goes on in your area can be difficult and time-consuming. And if you lack insight into your on-site assets' current location and status, it can lead to missed deadlines, poor customer experiences, and lost revenue.
Keep reading for how a track and trace process can transform your yard management, along with tips for implementing one.
Legacy yard management systems often are cumbersome, relying on manual asset tracking activities to manage the inbound and outbound flow of a yard. The manual nature of the system introduces several potential errors that can have a direct impact on a company's profitability, including lost or misplaced assets, incorrect inventory/asset counts, delayed shipping times, and inefficient communication workflows.
A modern inventory management platform featuring a track and trace process addresses these challenges. Automating the time-intensive task of managing your inventory offers two critical advantages – speed and data. With precise location tracking and detailed visibility into your inventory available at a single click, you and your team can turn your attention to more pressing business priorities. And with this additional data about your inventory integrated with your existing systems, you can more easily and quickly identify money-saving operational improvements.
Here are five steps to guide you through implementing a modern asset tracking process:
1. Determine what needs to be tracked
The first step is to determine what assets need to be tracked. This could include incoming and outgoing shipments, vehicles in the yard, and inventory storage locations. By keeping track of these critical elements, yard managers can ensure they are developing a system that will meet their specific needs.
Consider near-term future needs – you want to ensure that any process you implement will scale to meet the yard management needs of the following year or even the year after.
2. Select a system for recording critical asset information
Once you clearly understand your tracking needs, it's time to select a technology partner that can meet your unique requirements. There are a variety of solutions on the market that record asset information that run the gamut from barcode scanners and RFID tags to advanced geo-fencing and on-asset sensors.
These tools can quickly and efficiently track inventory levels and provide valuable insights for forecasting future demand and streamlining operations. In short, investing in a reliable tracking system can save time, boost efficiency, and ultimately increase profitability.
3. Train your employees in proper usage of the tracking system
After implementing your new tracking system, it's time to train your employees on its benefits and correct usage. Accurate data collection is crucial for a successful yard management tracking and tracing program, and your employees must be comfortable using the new system.
Make it easy for your employees to use the new system by selecting a system that:
- Offers an intuitive interface
- Minimizes costly training sessions
- Integrates with your ERP system
- Automates your manual tracking workload
A key driver for choosing a modern tracking system is eliminating as much manual burden as possible from your legacy system so that your team can work on higher-value tasks.
4 – Regularly review and update your new tracking system
As with any new system, you may experience minor growing pains.
An easy way to prevent them is to review your new tracking system and processes at regular intervals post-launch to ensure your new tool will continue to meet the evolving needs of your yard team and customers:
- Are any new developments or changes in the industry that could affect your operations?
- Is there a more efficient way to track crucial information?
- Are there new system tools or features that should be implemented to improve asset flow?
- Is your team experiencing realized efficiency gains in locating assets?
- Do your workflow metrics indicate the system is operating at peak efficiency?
By routinely assessing your new system and updating when needed, you can continue to streamline and optimize your yard management process.
Though it may seem like added work in the short term, investing time in this review process can save you trouble and headaches down the line.
5. Use the collected information to analyze and improve yard management processes
As any yard manager knows, inefficiencies can quickly add up and lead to lost shipments and profits. By collecting yard data and analyzing it regularly, it’s easier to pinpoint areas for improvement and track their progress over time. For example:
- Tracking shipment arrival times can help managers identify what times of day are busiest and adjust schedules accordingly.
- Keeping tabs on truck loading and unloading times to make sure they are maximized.
- Looking at how often shipments are misplaced or damaged can also reveal weaknesses in storage methods or communication processes.
With this information, yard management teams can work towards streamlining their processes and boosting overall efficiency.
Smarter Inventory Management
Increased operational efficiency is key to maintaining a competitive edge in a challenging economic climate. If your current yard management system relies on manual inventory checks, consider upgrading to a tech-based solution modern inventory management platform like GearTrack that automates your current workflows and gives you critical business intelligence. While implementing a track and trace process might feel daunting, proper planning and execution can significantly improve the efficiency and accuracy of yard management for your business.
Learn more about the many ways GearTrack can take your yard management to the next level here.